CSMCRI at Bhavnagar in Gujarat has developed a process to recover both SOP and MOP from the spent wash ash
11 May 2023
News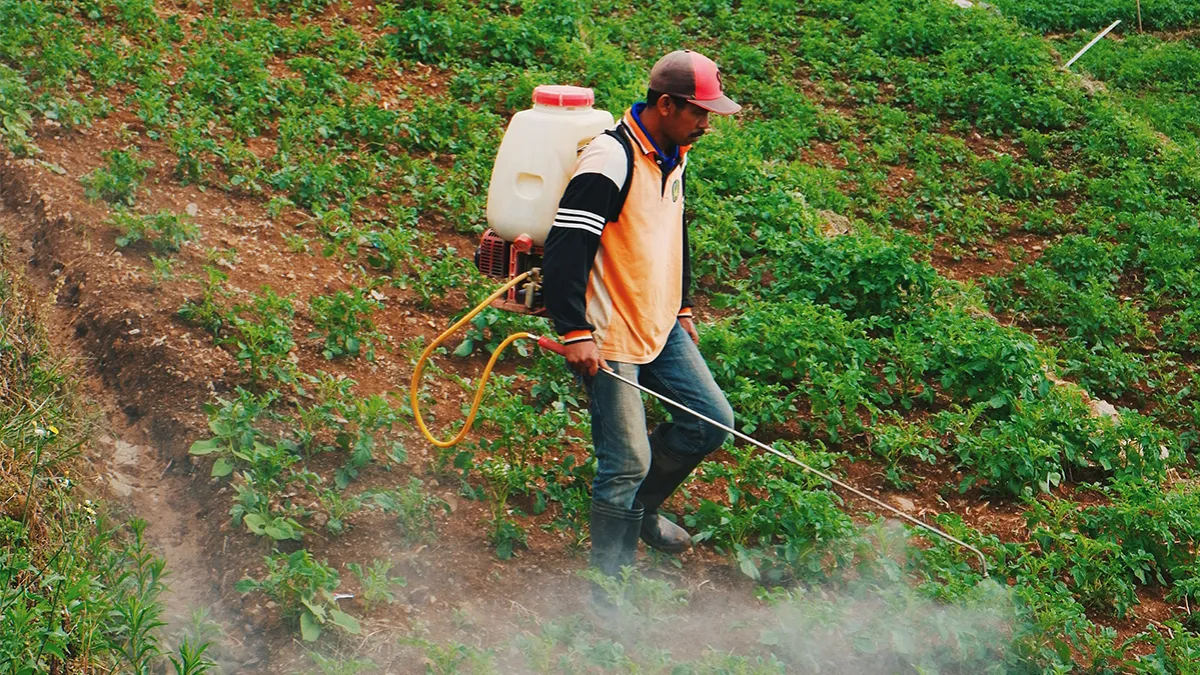
Here's a potentially game-changing technology for a country that has hardly any mineable potash resources and spends $1-1.5 billion yearly to import over 3 million tonne (mt) of this fertiliser.
A method to recover both sulphate of potash (SOP) and muriate of potash (MOP) from the leftover wash ash produced by distilleries using sugarcane molasses has been developed by the Central Salt and Marine Chemicals Research Institute (CSMCRI) in Bhavnagar, Gujarat.
One of the 37 top national labs operating under the auspices of the Council of Scientific and Industrial Research (CSIR), the primary institution for research and development that is led by the Prime Minister, is the CSMCRI. CSMCRI has licensed its technology to DCM Shriram Bio Enchem Limited, which is installing a plant based on it at Hariawan in Uttar Pradesh’s Hardoi district. The leftover wash ash from a 200 kiloliter per day distillery connected to a 13,000 tonnes cane per day sugar mill would be used in this plant, which will cost Rs 57 crore. A firm representative predicted that it will be functioning by August.
Basically, spent wash is the wastewater or effluent that is produced as a byproduct of making alcohol. For every one litre of alcohol that they create from fermented cane molasses, distilleries generate 10-15 litres of discarded wash. This effluent contains salts, vast amounts of organic matter, and roughly 2% to 3% potash, which, if dumped without treatment, can contaminate both land and water sources.
In India, 325 molasses-based distilleries produce 50 billion litres of wastewater annually in addition to 35 billion litres of ethanol. The Central Pollution Control Board has mandated that distilleries adhere to zero-discharge norms, so they primarily use two strategies to manage spent wash.
The first is by blending it with press-mud from sugar mills, the leftover cake after cane juice has been clarified and filtered. This combination is subsequently decomposed and transformed into manure. The second technique involves concentrating the used wash to 58–60% solids before feeding it into an incineration boiler. The final ash that is produced by the boiler includes 20–21% potash, and in certain circumstances, it is processed into granules for use in agriculture.
From distillery boiler ash, the CSMCRI technique may recover up to 90% of the potash. The usual recovery composition is around 55% in the form of SOP, 10%–20% as MOP, and 10%–30% as edible mixed salt. The ratio of SOP and MOP varies depending on the wasted wash quality. Leaching processes are used in the technology to separate non-salt solids from used wash ash, which is then transformed into bricks for masonry work.